New IT system delivers real-time data to the gemba
In New Britain, Connecticut, a scant 20 miles from major customer Pratt Whitney, is the new home of aerospace producer Polamer Precision, Inc., a first-tier high growth supplier founded by 52 year-old immigrant Chris Galik. Polamer Precision is a young company experiencing aggressive growth supporting major OEMs and their partners—General Electric, Hanwha, ITP and others.
Chris Galik and a machinist look at design schematics from Plex at a workstation.
“We’re competing successfully now not just in the U.S.—our competition is China, Japan and Poland. Based on innovation and automation that we heavily invested in, we’ve been able to reduce cost and pricing, and we’ve been able to get long term agreements,” CEO Galik proudly points out.
Related Articles
This is the first of a series of articles about manufacturers' use of the latest IT systems. Please see the other articles in the series:
But Polamer Precision’s business calls for incredible variety and very high quality. “In terms of SKUs, think of automotive, but with more complexity,” says Galik. “We know that our IT system can handle that kind of volume, with about 1,200 SKUs on average and 771 suppliers.”
Galik speaks frankly about the IT challenges his industry faces daily in workforce, as well as systems areas. “Our workforce is critical to our performance, but we know we cannot have unlimited headcount. In this very demanding industry, the people we need to contribute to our success, from machine operators, engineering and IT to purchasing and supply chain, Plex Systems helps us reduce headcount quite dramatically. We are pushing to have Plex directly dictate scheduling daily, to remove human error.”
Galik believes that the company’s system allows Polamer Precision to do customization that other software providers don’t. “The system has enormous capabilities. We do things differently at Polamer Precision, and we were attracted to this software because we knew we would be able to tailor it.”
The IT software changes were not easy, however. Although the current package has been in place for over six years, when Polamer Precision began the process, the company was a seventy-five person organization supported by some Master Scheduling and a few other software basics.
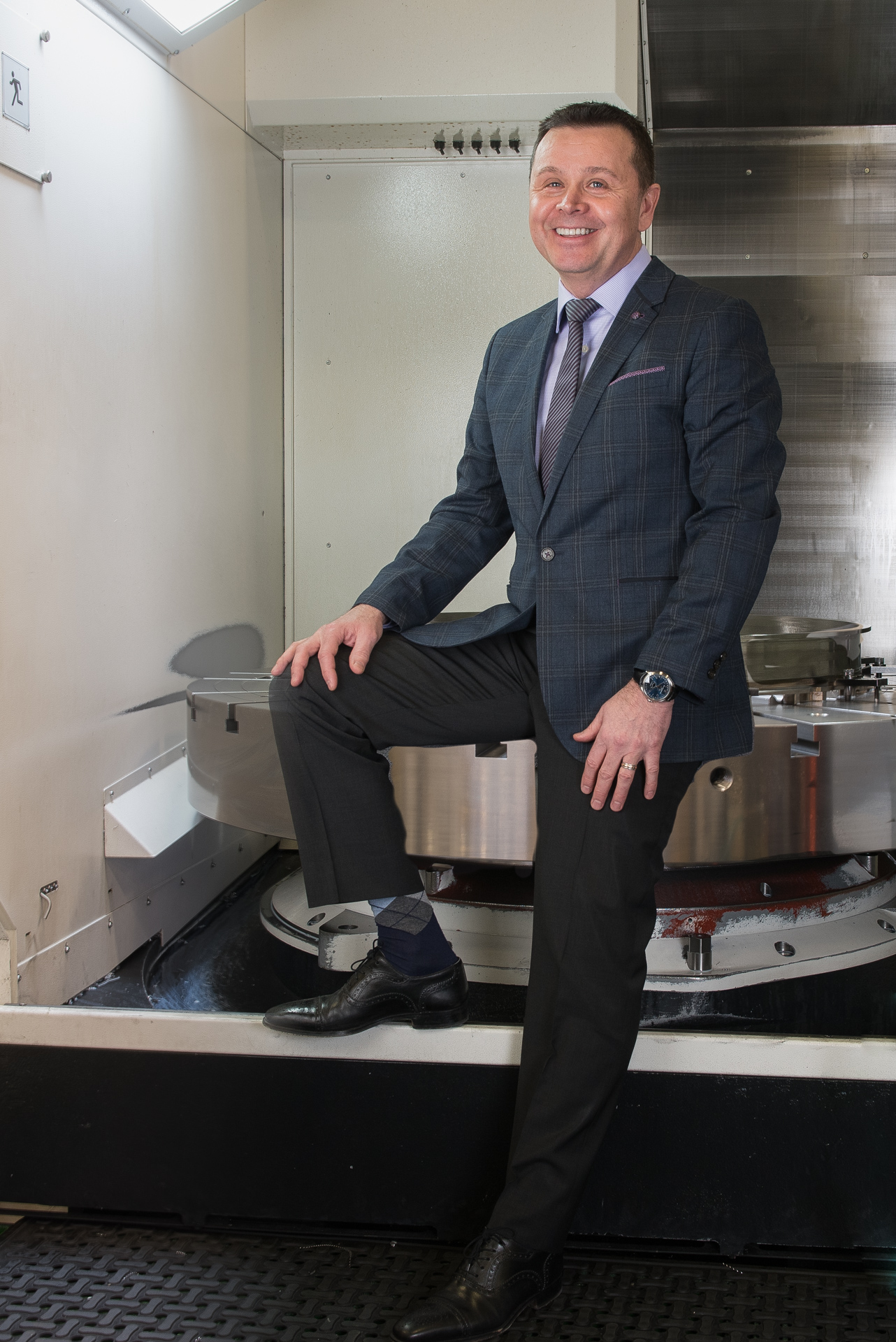
Chris Galik sitting inside one of Polamer Precision's many large 5-axis workcenters. About the company's transition to new IT, Galik said: "Sometimes the decisions are not always clear—you have to move where your future is. Did I know this new system would be so challenging? No. We knew what we were trying to establish—we are doing a lot of automation that ultimately communicates with Plex on a daily basis. It’s almost as if when you develop the next thing, you’re trying to see what else can be done with the system. The software is a living entity, and we know that the implementation will never end; we won’t hit the limits."
“This was not an easy choice for a company of under one hundred people, Galik said. “We definitely struggled a little at the beginning and we knew we needed people in the company who would be able to handle the transition. If you know your projected growth, you have to go with it.”
Before the new systems, the company used some ERP modules, with Quickbooks and JobBOSS for Master Scheduling. However, “We couldn’t handle it, so the old patched together systems were short-lived,” he said. The company looked at Oracle solutions and others, “but the cloud aspect of Plex and potential expansion and customization made the decision very easy.”
Galik sees changes in aerospace that parallel automotive’s transformation from a narrow industry sector populated by fewer key basic assemblies, to manufacturing marked by great variety and mass customization. The number of SKUs and parts quantities has increased. Although Polamer Precision invested in different software products that automotive had already been using for some time, Galik knew that, for growth, the company had to reach beyond automotive solutions, investing heavily in advanced new robotics and automation.
Polamer Precision’s organizational structure has been redesigned to support new technologies as well, with IT hosting a distinct and separate area called the Technology Department, where the Plex software is tailored to the company’s system’s needs. “We found that various ERP packages would not allow this, and to compensate for this limitation, other companies would have to hire an army to support IT.” In total nine people support IT inside Polamer Precision, three of whom maintain general IT, plus six in the Technology Department, where custom applications are developed and tailored to communicate well with Plex.
Lean vs IT?
The systems at Polamer Precision may operate quietly in the background, but on the floor, every individual has access. The operation is paperless—don’t expect to see paper drawings or prints because they appear and are used on Plex screens at every machine. To illustrate, Galik points to SPC (statistical process control). Detailed quality data might be collected for compilation and analysis by other companies in a month-long routine, but at Polamer Precision, that same information is available in one click as live, real-time data.
That’s where Galik sees the system enabling the company’s lean approach. He credits advanced IT for raising annual revenue per employee to over $260,000; in contrast, he sees traditional manufacturing running at $190,000 to $200,000 per year, per employee. The goal is to maximize every dollar of sales and, in 2018, Galik expects to reach $300,000 per employee.
Also, without the kind of advanced manufacturing IT Polamer Precision has developed, the company could not continue its pattern of doubling growth every two years, a trajectory that is projected to continue through the end of 2019 with the current customer base.
The IT challenge
“Sometimes the decisions are not always clear—you have to move where your future is. Did I know this new system would be so challenging? No,” Galik said. “We knew what we were trying to establish—we are doing a lot of automation that ultimately communicates with Plex on a daily basis.”
He added: “It’s almost as if when you develop the next thing, you’re trying to see what else can be done with the system. The software is a living entity, and we know that the implementation will never end; we won’t hit the limits. But in the end, it’s easy—pull out your laptop or tablet, and make the factory work, see the operations from anywhere.
Named a “Pioneering Woman in Manufacturing” by Fortune magazine, Patricia E. Moody (tricia@patriciaemoody.com) is a manufacturing management consultant and author.