Who's going to run the machines that make the machines? Asked another way, what kind of learner are you and your teams? Online digital or real-time hands-on contact, or a combination?
Increasingly, the ideal appears to be a combination of both because both learning avenues feed different needs in individuals. For instance, AME offers it annual Excellence Inside Conference in addition to regional meetings and plant tours. (This year, AME will hold its 30th annual International Excellence Inside Conference in Jacksonville, Florida, where you can learn from practitioners and walk the gemba walk with your peers Nov. 10-14. Visit www.amejacksonville.org for more session and schedule information.)
AME’s events offer hands-on learning opportunities. Attendees have the prime opportunity to meet with colleagues who have been in your shoes and who may have experienced something you are currently facing in your job. These shared learning opportunities spark ideas and provide answers to nettlesome questions.
Other ways to learn are via digital. We all love TED talks (see How to Deliver a TED Talk), Netflix and YouTube. This complements other learning opportunities that provide the training and workforce development the U.S. needs as we bring back manufacturing and scale-up to fill the roughly 600,000 vacant manufacturing jobs.
In addition to four-year degree programs, there is a need for live and digital learning options. Some added “coursework” could be provided via digital, particularly for difficult jobs to fill including machinists, toolmakers, mold makers, CNC programmers and technicians. Although some of these openings are replaced by automation, we still need trained, dedicated workers to run the machines.
Digital supplemented with live experiential learning — apprenticeships with coaching — could be an effective, cost-effective approach to massive workforce development. Kevin Meyer, co-founder of Gemba Academy and a veteran of both startups and a medical device company, began to see opportunity in the broad landscape of continuous improvement training.
Five years ago when Meyer, Ron Pereira and Jon Miller launched Gemba Academy, they created an approach based on a web-delivery model. The team set out to simplify life — “no tracking of individual usage, number of individuals consuming the content, etc.” The content — topics such as SPC and lean accounting — found a receptive Internet audience. Since the company launched, the academy grew to a 1,000-member online user community extending beyond manufacturing operations to health care, government and other industries. Meyer was surprised to see that although the original target audience had been smaller manufacturing operations, a funny thing happened.
“Instead of our customers being primarily smaller manufacturers, a majority now come from larger non-manufacturers. Lean and six sigma methods can be deployed anywhere — hospitals, law firms, defense, government, you name it. And it turns out that the large multisite organizations have many issues with communication and deployment of new concepts. That’s where an Internet solution that could be easily deployed across large organizations with different geographies and languages just as easily as at a single site, made sense,” Meyer said. Early offerings were conducted in English; Chinese and Spanish followed shortly thereafter.
Other valuable lessons appeared from bringing together global communications and delivery. Communities, or learning networks, formed over common interests. Participants learned that they could find their level and drill down on the specific tools and topics that they needed most. And there was collaboration.
“Communication begets collaboration,” said Meyer, “which encourages learning, reinforcement and better execution. So over the next three to five years, I see lots of potential in digital learning and collaboration technologies to enable professionals at all levels within and between organizations and industries to dynamically share, collaborate, learn and execute.”
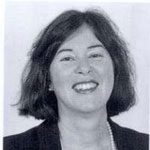
Named by Fortune magazine a "Pioneering Woman in Manufacturing," Patricia E. Moody, The Mill Girl at Blue Heron Journal, tricia@patriciaemoody.com, is a business visionary, author of 14 business books and hundreds of features. A manufacturing and supply management consultant for more than 30 years, her client list includes Fortune 100 companies as well as start-ups. She is the publisher of Blue Heron Journal, where she created the Made In The Americas (sm), the Education for Innovation (sm) and the Paging Dr. Lean (sm) series. Her next book about the future of manufacturing is The Fourth Industrial Revolution. Copyright Patricia E. Moody 2013. With permission.