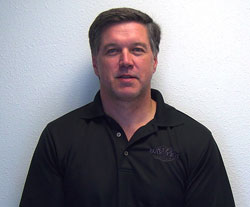
“Work hard, play hard — it’s not work when you’re having fun.” Those are great words to live by at Bay Tek Games Inc. in Pulaski, WI. Employees at the manufacturer of coin-operated redemption games understand how to improve their winning ways through lean improvements. Along the way, they’re also kicking up those initiatives a notch by participating in lean consortium activities. The company is a member of the AME Northeast Wisconsin Silver Consortium.
“We’ve hosted consortium tours here, highlighting our best practices, such as the visual factory. Our learnings also included visits to other plants,” said Kyle Berger, continuous improvement (CI) coordinator. “During the monthly meeting, a host company typically tells what they’re successful at.” Host sites also receive fellow members’ feedback, including improvement suggestions from noncompetitor organizations.
Berger noted the value of consortium tour site hosts candidly sharing their challenges as well as achievements during the events. In turn, when Bay Tek Games hosts such tours, employees gain helpful feedback, such as improvement ideas, from participants. “People can get a good grasp of our process when they visit,” he said of the facility’s visual management. “Even when we bring in people who are new, they understand where the game starts.”
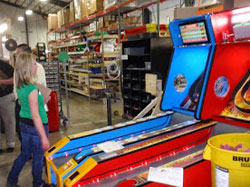
When you’re visiting other consortium members’ plants, expect to gain insights from their improvement initiatives, and be willing to provide feedback about opportunities for enhancing performance, Berger said. “In the past year, we’ve worked on our 5S program, taking some learnings from some of the consortium members’ tours,” he said. “We call our program 6S because we include safety. We’ve also had some good sharing with other companies, such as Douglas Dynamics (a plow manufacturer) in Milwaukee and Ariens, that do mixed modeling through the consortium. We sent two groups, including sales and our president, to Douglas Dynamics to see how they level loaded their schedule and kept inventory low.
“The greatest benefit from participating in the consortium is expanding our network in sharing best practices,” Berger said. “There’s no better way to learn than to see, whether a company is in manufacturing or a service industry. We’re all on the lean journey.”
The Improvement Journey Continues
Learning from the improvement experiences and results achieved at other consortium member companies supports Bay Tek Games’ long-term, organization-wide commitment to lean and CI improvements, said Pat Scanlan, manufacturing manager. Scanlan noted that Bay Tek Games has held consortium events on Total Productive Maintenance (TPM) from startup to shutdown and other topics.
Bay Tek Games tracks five operational metrics: quality, safety observation submissions, CI idea submissions, 6S scores and productivity internal feedback. Suggestions from consortium members support the company’s day-by-day improvement progress. Among the company’s initiatives: boosting productivity (reducing the minutes per move between each of 12 workstations), improving safety performance and greater CI participation. Implementing a financial incentive program linked with performance for each metric highlights the CI focus. Results are tracked monthly, and payouts are made every four months. In the spirit of CI, tougher goals are set each month for these metrics.
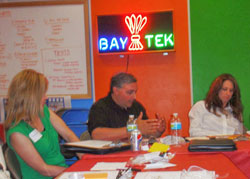
For Larry Treankler, chairman of Bay Tek Games and sister company MCL Industries Inc., the lean consortium makes sense as Bay Tek Games continues to gain CI momentum. A former fan of batch building, Treankler initiated lean improvements within the company in 2003.
“We had hit a wall that year,” he said. “We were out of space; we had $2.3 million in inventory and 14- to 16-week lead times. We were growing the business and going out of business at the same time. We were working on a model that was unsustainable.”
While the company had developed market winners in specific games, its lead times and inventory costs continued to grow.
Working with the Wisconsin MEP (Manufacturing Extension Partnership) and Optima consultants, Bay Tek Games began its lean journey.
“We also created a leadership group, and we started systematically mapping all areas of our business beginning with manufacturing,” Treankler said. “It took a little while for manufacturing employees to change from three or four (dedicated) lines to embrace more product knowledge. They had to know about 24 titles rather than just six. By the end of two years, they were giving us more improvement ideas than we can implement at one time. Three years later, our sales had grown 100 percent, we didn’t add to our building, and our sales were at $19 million. We could go to $30 million with no increase in our space.”
Now 24 products all go down the same line.
Lea Tonkin, president of Lea Tonkin Communications in Woodstock, IL, is the former editor in chief of Target and Target Online.