![]() |
Doman: Process map with a purpose. |
This is the time in the semester when my Oakland University students are completing their Lean Workouts and submitting their process maps of the current state.
Invariably, they ask me the following questions:
- How many steps should we show on the process map?
- What should be listed as a step?
- Is this a value-added step or is it waste?
- Where does the process start and end?
Because I want to reinforce that process mapping is a lean tool with a purpose and not a collection of boxes and arrows, I always answer their questions with my own set of questions:
- What is your purpose for doing this process map?
- What are the problems you are looking to solve: quality, cost, delivery?
- How do you know what the problems are?
- What are the metrics (if any) that tell you what the problems are?
- Did you go to the gemba and really observe what was going on, or were you an industrial tourist just strolling through the plant?
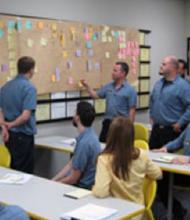
Figure 1. Fitzpatrick Manufacturing team process mapping.
I require them to answer my questions with data and facts. I remind them that I don’t want to hear their opinions or anecdotes from the floor or “sunshine news” from management. I push them to dig in and get the facts to understand what the real problems are so they can answer their own questions about how to go about mapping the current state of the process.
For example, one of the student teams is working on the finished goods inventory and shipping processes for a sponsor company. The problems the sponsor identified for the team mostly involved quality and delivery to a major customer. The sponsor company was too often shipping the wrong parts, shorting the order or not finding the parts for the order and then scurrying to run a batch of the right parts at the last minute.
In the team’s presentation, they described the problems and then showed their current state process map, which was basically a one-page overview or “flyover” of the final good inventory and shipping process. Not good. Not even close to zeroing in and using the process map as a tool to identify the steps that are contributing to the problem and contain the most waste.
When the team’s presentation was finished, I asked them another battery of questions focusing on the problems and getting them to roll up their sleeves and dig deeper into what is actually being done in the process:
- Did you actually walk the process and follow the high/low drivers, shipping personnel, customer service personnel, etc., for an extended period of time and on different shifts?
- Did you do a deep dive into the major steps that you thought contained the most waste and/or contributed most to the major problems?
- Did you identify and verify each and every activity that employees were doing in these areas, especially the defect correction loopbacks?
- Did you talk to the next-in-line process customers to determine exactly what their requirements are and whether these requirements are being met on a consistent basis?
I asked these questions because if the answers to these questions are, “Not really,” then your process map is a nice collection of obvious steps, but not much of a lean tool to reduce waste and solve the problems in the Lean Workout.
Like any lean tool, process mapping is not a quick exercise in identifying the surface of a situation. It should be used as a high-powered lens to see exactly what the current state is and uncover waste. Only then will your team be able to determine root causes and advance countermeasures to solve the problems.
Process maps are lean tools to be used for a purpose. Use the lean tool to help you solve the problems. If your use of the tool doesn’t do that, you’re either using it incorrectly or not diligently enough or you need to use another lean tool.
About the Author
Doman is a Pawley Professor in Lean Studies at Oakland University in the Organizational Leadership Department and a member of the leadership team at the Pawley Lean Institute.