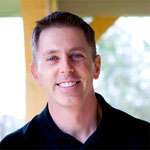
Have you had the experience of being told exactly how lean should be introduced and rolled out, to the extent that the entire process seemed a bit militant? As lean is based in methodology, there are dozens of instructors and practitioners who are absolutely stuck on following a six-step process for this or a 10-step process for that.
Don’t get me wrong, I’m not a fan of shortcuts. That is, unless the shortcuts are likely to demonstrate improvements that can be further enhanced once in place. I’m not suggesting an “act now, think later” approach, but I am suggesting that overthinking or overanalyzing can waste time, and when introducing lean and attempting to achieve results (and gain engagement in the process), time is of the essence.
I remember participating in some Six Sigma training about 10 years ago during which we were shown a plethora of formulas, all culminating to a final project that had to be submitted. Although the formulas made sense, the practicality in some instances didn’t. I recall the instructor telling me, “No, you have to do it in this way, just to prove your results.”
In my experience, there are only a few key points that should be kept in mind as relates to lean:
- Value is in the eye of the customer. Ultimately, anything that the customer isn’t willing to perceive as valuable (or willing to pay for) is waste and should be reduced, minimized or eliminated. Have you actually talked to your customers lately to understand what they value?
- Collaboration is key to success. Lean is about employees coming together to improve what they do and how they do it. This isn’t a management initiative, nor should it be, but managers should still be part of the process; after all, they are employees too.
- Common sense prevails. If something feels or looks burdensome, it likely is. You don’t need to hold a meeting to discuss every little change, nor do you need to wait until the next kaizen event comes along. The premise of lean is to get employees thinking and acting in a way that improves business performance and efficiency. Allow them the opportunity to apply their common sense, and you will see rapid improvements without having to influence their introduction.
- Industry best practices don’t always fit. It’s quite common for managers, suppliers and executives to thrust change upon employees with the desire to achieve higher levels of productivity. However, this is often done through the incorporation of new software, technology or equipment that is not built specifically for the business. Just because new technology or equipment is considered “industry best practice” doesn’t mean it’s the best practice for your business. Engage employees in identifying new solutions based on their existing needs, and you will find a faster and more effective rate of adoption.
- Obsession in 5S can be unproductive. I’ve met dozens of plant managers absolutely obsessed with 5S. You can almost hear them chanting under their breath, “a place for everything and everything in its place.” Let’s face it, there are hectic times in any business where 5S may not take a front seat, and that’s okay. The premise with 5S is to organize the workplace to minimize travel, waiting time and duplication. Being fanatical about it can be wasteful.
With these points in mind, consider your own lean initiatives. Have you stumbled to get your initiatives off the ground or adopted by employees? Consider how adamant you or other resources supporting you have been that a “method” must be followed. If you realize your approach was heavily based in methodology, come back to the basic premise of lean such as those found above and renew your efforts.
After all, we are looking for incremental improvement, not regimented improvement.
Casemore is the president and founder of Casemore and Company, a management consultancy helping organizations globally to improve organizational performance and build financial strength. Learn more at www.casemoreandco.com or follow Casemore on Twitter @ShawnCasemore.